If you look at the latest electronic equipment, you’ll find that it has many components. One of the most important is the printed circuit board (PCB). Every device you use, including your smartphone, personal computer, or even a microwave oven, has printed circuit boards. The miniaturization of electronic devices makes standard methods of mounting electronic components on the PCB surface unsuitable, which is why OEMs are increasingly choosing to assemble SMT. What is this method characterized by, and when should it be used? A few words about it in the article below.
Thanks to surface mounting technology, it is possible to build even the most complex electronic boards with great ease. In addition, using this technology, OEMs can obtain smaller assemblies with excellent repeatability. That is all thanks to surface mount technology’s high automation and precision. So let’s find out what SMT is in detail and its benefits?
SMT assembly: Definition
Surface mount technology, or SMT, is how electronic components are placed directly on a printed circuit board’s surface or PCB. It is essential that, unlike Through-Hole Technology (THT) assembly technology, SMT allows the placement of elements on both sides of the PCB, thanks to which electronics manufacturers can use the surface of it much more effectively. As a result, many manufacturers now use this technology to enable the rapid design of small, light, and compact printed circuit boards. Best of all, it is a much faster process compared to through-hole technology.
Of course, SMT technology requires appropriate technical facilities associated with a significant investment in the entire machine park. However, what should be emphasized, surface mount technology also distinguishes from THT the possibility of automating the whole process. Together with better-developed PCB surfaces, SMT assembly can ultimately benefit manufacturers. Therefore, it is not surprising that it is currently the most frequently chosen assembly type.
Here you can find more information about Surface Mount Technology (SMT): https://asselems.com/en/smd-assembly
MATERIALS USED IN SMT ASSEMBLY
As you can read above, assembling electronics with the surface method requires a very extensive machine park. However, this is not all. To be able to implement SMT assembly, it is necessary to have materials dedicated to this method, which include:
- Printed circuit board: An element made of a suitable insulating material, covered with a conductive foil. Electronic components located in a given device are mounted on the SMT
- Solder paste: It’s nothing more than a mixture of flux and small solder particles. In the case of SMT, a paste mixed with tin alloys is used
- Cleaner: It’s a substance based on isopropyl alcohol, used to clean elements, so-called “wet”
The course of SMT assembly
SMT is not a complicated process; however, as you can probably imagine, it requires appropriate knowledge and experience. Each PCB assembly provider can carry out the assembly slightly differently, but the SMT process consists of six basic steps in most cases.
#1: PROGRAMMING
Before starting the assembly of STM, the manufacturer configures all machines to adjust their parameters to the specifics of assembly of a specific device with PCB. In the case of working with professional PCB Assembly suppliers, you may come across the statement that EMS uses Gerber data. These are the data required to manufacture the PCB. Often, CAD files are not available, and during the configuration of machines such as AOI (Automated Optical Inspection) or the Pick-and-Place machine, it is necessary to create a plan of their operation based on the data provided.
#2: APPLYING SOLDER PASTE
After programming the machines, the next step is to apply solder paste to the PCB on the appropriate fields of a single printed circuit board using a template and squeegee. Here, manufacturers use screen printing. This step ensures that the soldering of components to the PCB will be smooth.
#3: SOLDER PASTE INSPECTION
The solder paste inspection occurs throughout the entire process. For this purpose, OEMs or their EMS suppliers use 2D technology or dedicated SPI machines based on 3D technology. However, 3D solutions are much more effective because they allow you to generate a three-dimensional image of the tile’s surface. Thus you can verify the quality of the paste application, including its height, excess, deficiency, and identify impurities or bridges.
#4: ASSEMBLY OF PARTS
The next step in the SMT assembly process is carefully placing the components on the stationary printed circuit board. This assembly stage can be almost completely automated thanks to the pick & place machine, which picks up the appropriate element with a unique feeder, and then precisely places it in a dedicated place. Automation of the process allows the deployment of even 100 to 120 thousand components per hour, which is impossible with THT assembly.
#5: SOLDERING
When the components are joined, the following step is reflow soldering in a special soldering furnace. Reflow soldering ensures that the solder melts and connects to the PCB.
#6: AUTOMATIC OPTICAL INSPECTION
The final stage of SMT assembly is automatic optical inspection (AOI). The primary purpose of AOI is to verify both the quality of the weld and assembly. Then, with the help of several high-resolution cameras, printed circuits are scanned for the characteristics of the PCB surface. An automated optical inspection enables manufacturers to detect potential assembly errors early and prevent defective PCBs from entering the market. That is a must before the device goes into mass production.
SMT: why is it worth it?
SMT enables the development of thin, light, reliable, and complex-functions PCB for electronic products, for which the market demand is sure to increase even more in the coming years. An SMT component can weigh as little as a tenth of its regular pass-through counterparts. At the same time, SMT components take up little space on the PCB. There are also significant advantages to this assembly model in the production section. First of all, the choice of SMT in production lowers the cost of the PCB, reduces maintenance costs, and enables control of the production process.
Importantly, however, the above advantages of surface mount technology do not necessarily mean that SMT assembly will always be more cost-effective. For example, in the case of the PCB assembly, it depends on what company and how it will be responsible for the assembly. Undoubtedly, choosing an experienced and competent EMS provider can directly influence the entire project’s success and profitability.
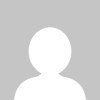