Ever walked into a food production facility and caught a whiff of lingering grease in the air? That smell, that film on equipment, even the subtle sheen on the floor… It’s all pointing to one thing: ineffective oil removal.
It’s not just about keeping the place clean. Choosing the right oil removal system has a direct impact on efficiency, safety, compliance, and the shelf life of your products. If you’re responsible for this decision, you’re not just picking a machine. You’re choosing how your facility runs day-to-day. So, what should you actually be looking for?
First, get clear on your waste profile
Before anything else, understand what kind of oil you’re dealing with and how much of it your process generates. Not all food processing oil removal systems are built the same, and they shouldn’t be.
Are you dealing with light surface oils or thick, sticky residue? Is the oil mixed with water, food particles, or cleaning agents? Is the output continuous or in batches? These are details that make a big difference. When you understand the characteristics of your waste stream, you can begin to narrow down your options.
Get Specific About Outcomes
Saying you want “cleaner water” or “better efficiency” isn’t enough. You need to define what success looks like for your facility. For some, it might be about cutting cleaning times in half. For others, it’s about meeting strict discharge limits. You might want to reduce how often you replace filters or improve conditions on the production floor.
When you have clear goals, you’re better positioned to compare systems based on what they’ll deliver, not just on spec sheets, but in daily use. That clarity also makes it easier to justify the investment, especially if you can link it to factors such as regulatory compliance or reduced downtime.
Choose a System That Fits, Literally and Logistically
The biggest mistake people make is trying to force a generic system into a unique operation. What works for one facility may be completely wrong for another, even if they produce similar products.
Before committing to anything, take a detailed look at how the system will integrate into your current setup. Will it fit in the space you have? Will it disrupt any existing workflows? Does it require additional staff or training to operate?
A system that checks every box on paper but creates bottlenecks or requires constant hands-on management will ultimately cost you more in the long run.
Maintenance Can Make or Break It
You can have the most efficient system in the world, but if it’s a nightmare to clean or constantly breaking down, it’s going to cause more stress than it’s worth. And if your team dreads using it, or worse, avoids using it altogether, that’s a problem.
This is where long-term thinking really matters. Look at the system’s maintenance schedule. Ask about cleaning cycles, filter changes, and part availability. A little extra time spent here can save you months of headaches down the line.
Don’t Forget the Bigger Picture
Oil removal doesn’t happen in a vacuum. It affects your water usage, your energy bills, and even the amount of waste you produce. Therefore, do not evaluate systems solely based on oil removal. Look at how they interact with the rest of your operation.
This is especially important if you’re working toward broader goals, like reducing environmental impact, minimizing water waste, or preparing for future facility upgrades.
Keep in mind, the system you choose today should still make sense in five years. If you plan to scale up or change product lines, flexibility matters. Some systems are limited to a single function. Others can be adjusted to handle different flow rates or oil types. That adaptability can save you from a second major purchase down the line.
What to Prioritize
Once you’ve identified the type of oil you’re dealing with and how it fits into your production flow, narrow your decision by focusing on these five areas:
- Oil compatibility – The system must match the specific oil types and consistencies present in your process, whether it’s light, emulsified, or heavy grease.
- Throughput capacity – It should comfortably handle your peak production volumes without compromising performance.
- Maintenance demands – Look for minimal downtime, simple cleaning steps, and easily available replacement parts.
- Ease of integration – The setup should fit within your existing infrastructure and seamlessly connect with your current processes without requiring major rework.
- Operating efficiency – Consider the total cost to run it, including energy, water, and labor, not just the purchase price.
The Decision That Shapes Daily Operations
Oil removal might not be the flashiest part of food processing, but it is one of the most critical and quietly essential. Get it right, and everything else, from hygiene and safety to efficiency and compliance, runs smoother.
This isn’t just about finding a machine that extracts oil from water. It’s about choosing something that supports your workflow, keeps your team moving, and holds up under pressure day after day.
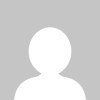